In the world of vehicle manufacturing, the quest for improved efficiency and strength is ongoing. One significant advancement in this field is the use of clinch nuts, which have revolutionized how vehicles are assembled. These specialized fasteners play a crucial role in joining metal components, offering numerous benefits over traditional methods. By exploring how clinch nuts improve efficiency and strength in vehicle manufacturing, we can understand their impact on the automotive industry. These fasteners contribute to faster assembly times, enhanced structural integrity, and overall cost reduction in vehicle production. As the automotive sector continues to evolve, with a focus on lighter, stronger, and more efficient vehicles, the role of clinch nuts becomes increasingly important. This article will delve into the types of clinch nuts used in automotive applications, their installation process, and the advantages they offer over conventional joining methods.
Types Of Clinch Nuts And Their Applications
Different applications in vehicle construction call for specialized clinch nuts designed for optimal performance. The main types used in the automotive industry include S, SS, CLS, CLSS, and SP. These different variants are tailored to work with various materials and thicknesses commonly found in vehicle construction. For instance, CLS and CLSS types are recommended for use in steel or aluminum plates with a hardness of HRB 70 or less. This makes them ideal for many body panels and structural components in modern vehicles. On the other hand, S and SS types are suitable for slightly harder materials, with a recommended use in steel or aluminum plates with a hardness of HRB 80 or less.
For more demanding applications, such as those involving stainless steel components, the SP type is recommended. This variant is designed for use in stainless steel plates with a hardness of up to HRB 90. In cases where softer materials are used, the CLA type is preferred, as it’s suitable for steel or aluminum plates with a hardness of HRB 50 or less.
The selection of the appropriate clinch nut type is crucial for ensuring optimal performance and longevity of the fastened joint. Factors such as the ductility and thickness of the metal, as well as the specific function the nut needs to perform, must be carefully considered. By choosing the right clinch nut for each application, manufacturers can significantly enhance the overall quality and durability of their vehicles.
Installation Process And Advantages Over Traditional Methods
The installation process of clinch nuts is straightforward and efficient, contributing to their growing popularity in vehicle manufacturing. The process begins with thorough preparation, ensuring that all tools and materials are ready for use. The fastener is then selected based on the specific application requirements, a critical step that enhances the performance and longevity of the joint.
To install the clinch nut, downward pressure is applied using a press, embedding the fastener into the material. After installation, it’s essential to verify that the head is flush with the top of the sheet and that the clinch ring is fully engaged. Regular checks for punch wear are also recommended to maintain installation quality.
One of the key advantages of clinch nuts over traditional welding methods is the significant improvement in assembly time. Installation of clinch nuts can be completed in just 10 seconds per nut, compared to 60 seconds for riveted nuts. This efficiency translates to a 30% improvement in assembly time compared to welded joints.
Moreover, clinch nuts maintain their strength and structural integrity over time, often outperforming welded connections. The faster installation time not only improves production efficiency but also reduces labor costs. The process is also more versatile, as clinch nuts can be set from either the top or bottom of the sheet metal, providing greater flexibility in assembly.
Improving Efficiency And Structural Integrity In Vehicle Assembly
The use of clinch nuts significantly enhances both the efficiency of the assembly process and the structural integrity of vehicle body panels. By mechanically locking together sheet metal layers without additional elements, clinch nuts improve the strength of joints. This method allows for the use of lighter materials in vehicle manufacturing, contributing to overall weight reduction, which in turn improves fuel efficiency and reduces emissions.
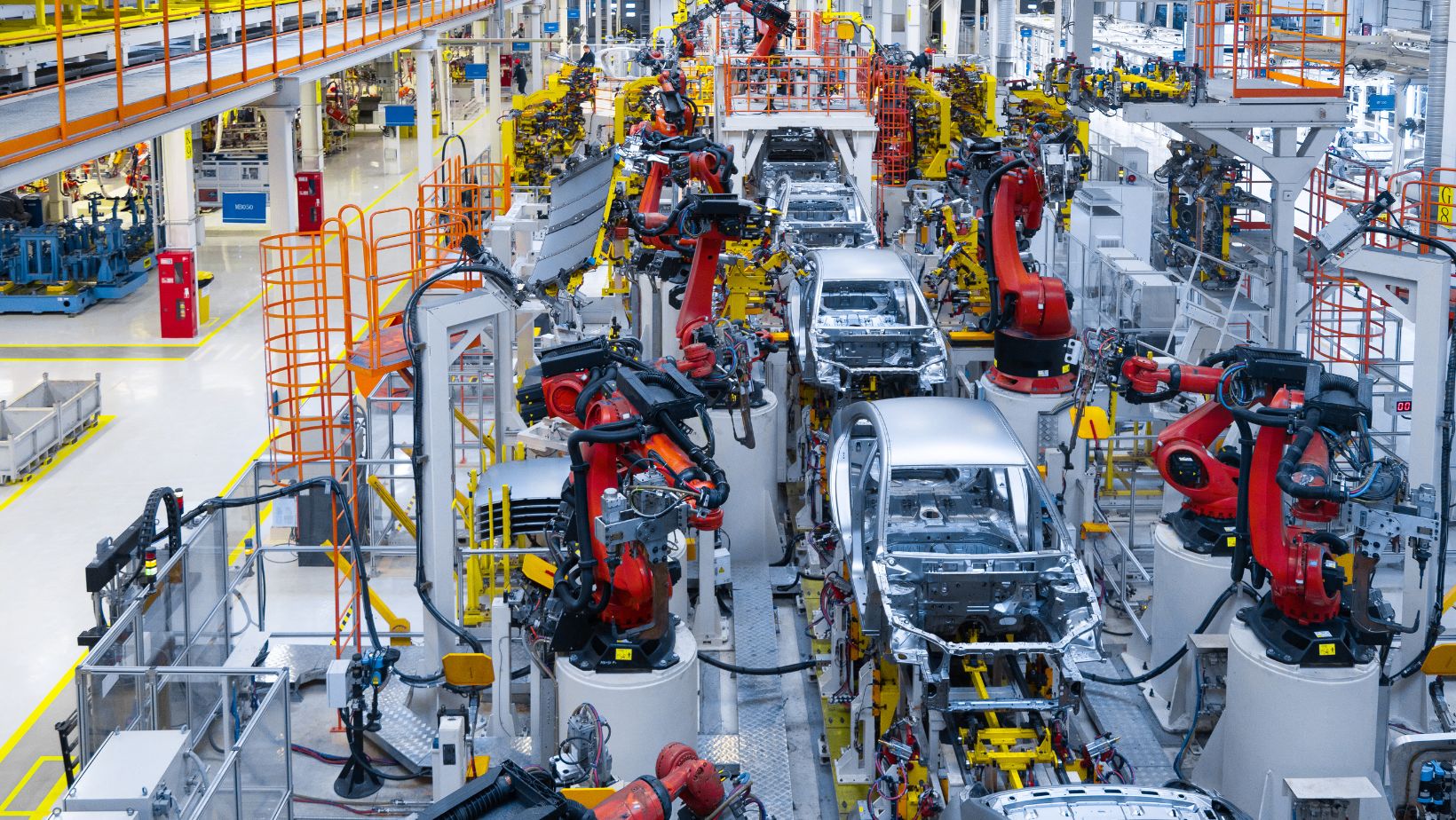
When properly executed, clinching can prevent crack formation, maintaining the corrosion resistance of joints – a crucial factor for the longevity of vehicle body panels. The long-term cost benefits of using clinch nuts in automotive production are substantial. They reduce manufacturing costs by eliminating the need for additional joining elements, and as tool life increases, unit costs decrease, making clinching a more economical option over time.
Furthermore, clinch nuts contribute to weight reduction by enabling more efficient and lighter assembly methods, allowing the use of thinner sections of stronger materials.
Innovations And Future Developments In Fastener Technology
The field of clinch nut technology continues to evolve, with new innovations aimed at meeting the changing demands of the automotive industry. For electric vehicles, new rotating and longitudinal symmetric self-clinching studs are being developed to provide reliable electrical connections in busbars with low electrical resistance for power systems. These advancements are crucial for the efficient operation of electric and hybrid vehicles.
Smart manufacturing technologies are also impacting clinch nut installation in automotive production. Tools like the HFC3000II and Micro-Nutrunner help prevent cross-threading during installation, while position-control torque arms improve accuracy and control. New materials are being explored for clinch nuts, with the automotive industry increasingly investigating the combination of high-quality steel and plastic materials for future vehicle production.
Companies like Facil, which specialize in fasteners for the mobility industry, play a crucial role in these developments. As a link between vehicle manufacturers and fastener suppliers, such companies drive innovation and ensure that the latest fastening technologies are available to the automotive industry.